開発力
加工現象をシミュレートするソフトウェアを導入しており、金属の変形量や金型への負荷値の情報を開発段階で得ることができます。
その内容を基に素早く金型・工程設計を自社で行う事により、他社では出来ない形状の加工を可能にしております。
内製によるノウハウの蓄積
自社で金型設計を行う事により、生産や金型の耐久性などのノウハウを蓄積し、より顧客満足が高い製造方法を後世に伝える仕組みを確立しております。
この独自ノウハウを駆使して顧客の要望に素早く応える体制が整っております。
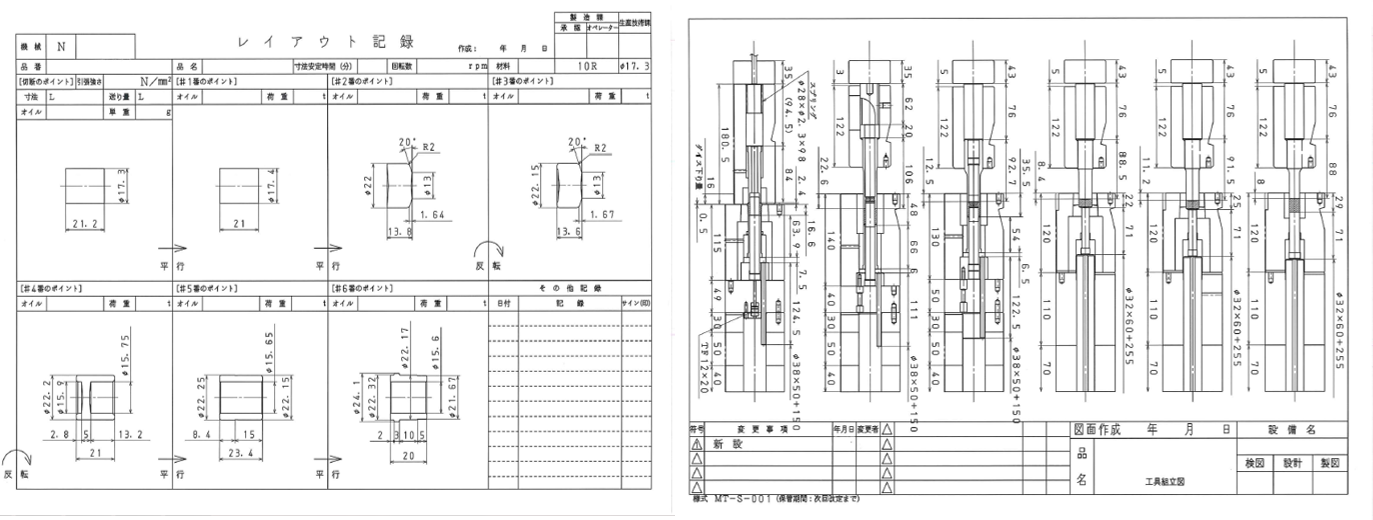
社内での圧造工程設計と金型レイアウト設計の事例
一貫生産体制による顧客ニーズへの対応
冷間圧造のみでは完成形状に出来ない部品でも、その後の切削、穴あけ、ねじ切り、洗浄、組付け、検査などの後加工も社内で一貫して生産することにより、数社に渡り加工する際の輸送費や顧客の管理工数の低減に貢献しております。
また、開発段階から量産時まで各工程での問題点を一括管理できるため、素早く問題解決することで工期の短縮を実現しております。
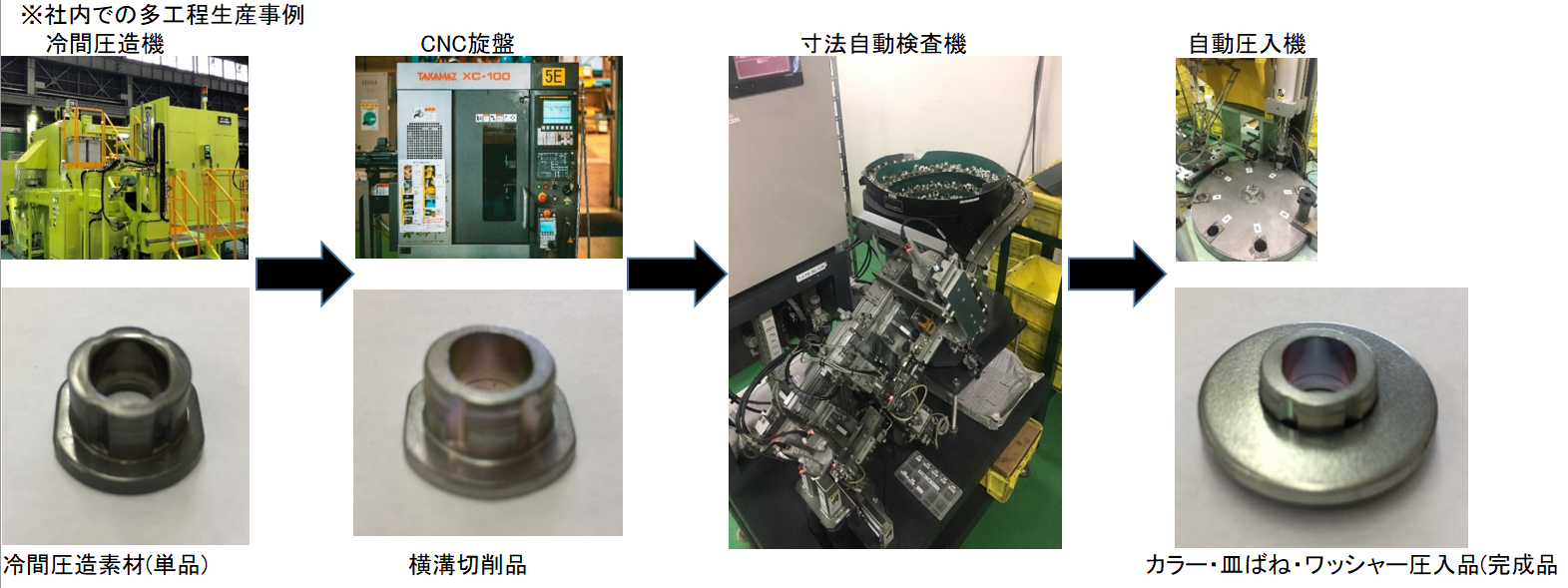
汎用設備の活用
汎用設備を使用し段取り替えを素早く行う事により、少量多品種ニーズにお応えしております。
段取り替えが多い機械では月に10製品以上の生産を行っております。
汎用設備を活用することにより初期投資を最小限に抑え、設備償却費用などが部品単価へ反映されることを抑え原価低減に繋げております。
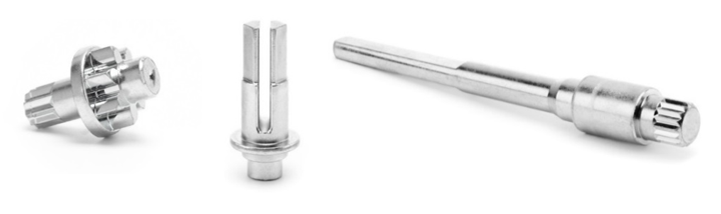
形状や太さ、長さは異なりますが、同じ設備で生産された製品です
ニアネットシェイプへの挑戦
シミュレーションやノウハウを活用して可能な限り冷間圧造のみでの成形を考え実現することにより、無駄な二次加工を削減して原価低減に努めております。
2部品の結合品や2工程で仕上げていた部品を冷間圧造工程のみで1部品化するVA・VE提案を積極的に行い、原価低減に繋げ顧客からの好評を得ております。
他社が「これは冷間圧造のみでは無理だ!」という難形状の部品を後加工無しで仕上げる強みが我社にはあります!
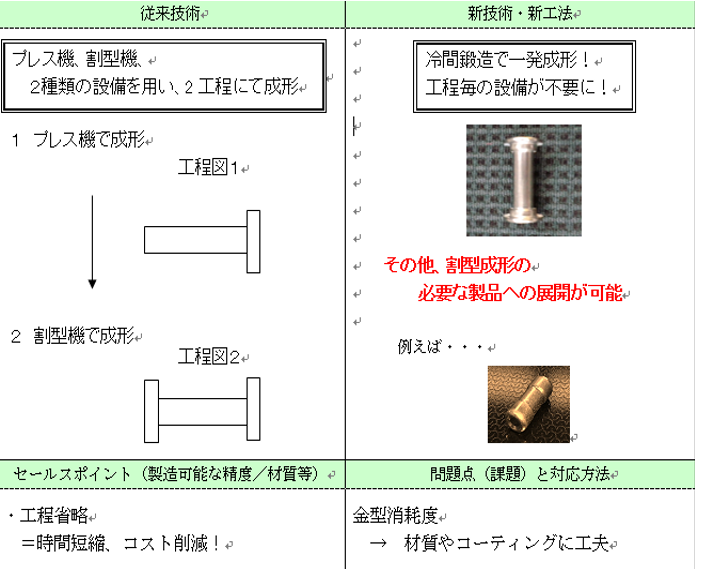
2工程を1工程へ工程削減した事例
QCD満足
顧客の品質要件を満たすためFMEAの実施、量産後の監視、出荷後のロットトレースもシステムで行い品質満足を実現します。
最適な工程設計をすることにより、適正な価格を算出します。
生産工程・在庫もシステムで一元管理して納期遅延などで顧客に迷惑をかけない生産管理システムを構築しております。
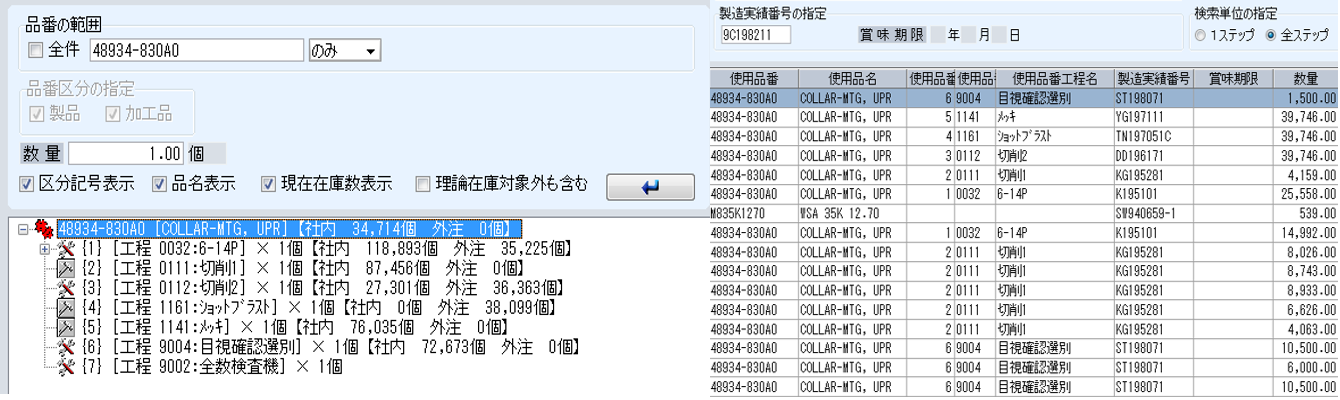
各工程での在庫数と各工程のロットトレースを一覧にした在庫管理システム